Welding processes significantly impact the quality of customized fuel tanks by influencing structural integrity, leak resistance, and long-term durability. Here’s how key welding factors affect tank performance:
1. Welding Method Selection
Different welding techniques yield varying results:
- Tungsten Inert Gas (TIG) Welding: Produces precise, low-spatter welds ideal for thin materials (e.g., aluminum alloy tanks). Its clean fusion minimizes internal contamination, critical for fuel purity in aviation or medical applications.
- Metal Inert Gas (MIG) Welding: Faster and more suitable for thicker steel tanks, but requires careful control to avoid porosity or undercutting, which can weaken seam strength.
- Laser Welding: Enables high-speed, deep-penetration welds with minimal heat distortion, critical for maintaining dimensional accuracy in complex tank geometries (e.g., curved baffles).
2. Weld Quality and Defects
Poor welding practices introduce defects that compromise tank quality:
- Cracks: Thermal stress during welding can cause micro-cracks, leading to fuel leaks under pressure. For example, stainless steel tanks may develop intergranular corrosion if welds are improperly annealed.
- Porosity: Trapped gas bubbles in welds reduce structural integrity. In marine tanks, porosity can accelerate corrosion from saltwater exposure, violating SOLAS safety standards.
- Incomplete Fusion: Inadequate penetration between metal layers creates weak points. Automotive tanks with such flaws may fail vibration tests (e.g., ISO 16750), risking fuel spills in collisions.
3. Material Compatibility and Heat Affected Zones (HAZ)
Welding dissimilar metals or improper heat control in HAZ can degrade tank performance:
- Galvanic Corrosion: Welding aluminum to steel without isolation layers creates an electrolytic cell, leading to rust and leaks. Aviation tanks avoid this by using monolithic materials or barrier coatings.
- HAZ Softening: Excessive heat in high-strength steels (e.g., ASTM A516) can reduce yield strength in HAZ, compromising pressure resistance. Narrow-beam techniques like electron beam welding minimize this risk.
4. Post-Weld Processing and Certification
Post-weld treatments are critical for quality assurance:
- Heat Treatment: Annealing welds in stainless steel tanks removes residual stress, preventing stress corrosion cracking in acidic fuel environments.
- Non-Destructive Testing (NDT): Dye penetrant or ultrasonic testing ensures welds meet standards (e.g., ASME BPVC Section V). For UN-certified transport tanks, 100% radiographic inspection of seams is mandatory to comply with hazardous material transport regulations.
- Surface Finishing: Grinding or polishing welds reduces fluid turbulence and corrosion traps. Marine tanks often require smooth internal surfaces to meet IMO guidelines for fuel cleanliness.
5. Process Consistency and Operator Skill
Inconsistent welding parameters (e.g., voltage, travel speed) or untrained operators lead to batch-to-batch variability. Automated welding systems (e.g., robotic arms with real-time arc monitoring) ensure uniform bead geometry and penetration, essential for large-scale production of tanks compliant with ISO 3834 quality management systems.
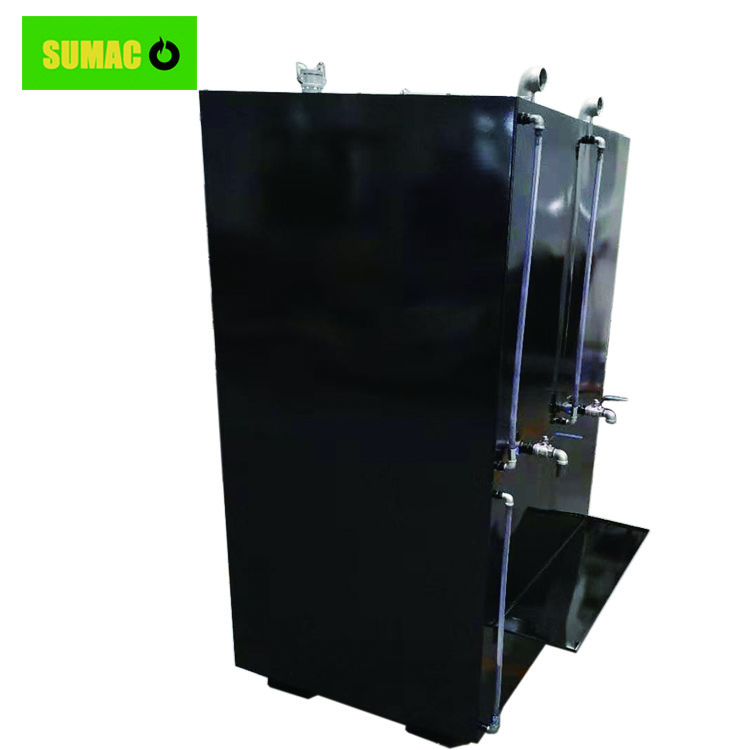