The pressure testing of fuel cube tanks is a critical procedure to ensure their structural integrity and safety during operation. A standardized process helps accurately assess the tanks' ability to withstand internal pressures without leaks or failures.
Pre - test Preparation: First, thoroughly inspect the tank's exterior and interior for visible damage, such as cracks, dents, or corrosion. Ensure all connections, valves, and fittings are properly installed and tightened. Connect the tank to a reliable pressure source, typically a hydraulic or pneumatic pump, and install accurate pressure gauges with appropriate ranges to monitor the pressure changes precisely.
Initial Pressure Application: Gradually increase the pressure inside the tank at a controlled rate, usually not exceeding 10% of the maximum test pressure per minute. This slow increase helps avoid sudden stress on the tank structure. During this stage, closely observe the pressure gauges and the tank's surface for any signs of abnormal deformation or leakage.
Holding and Inspection: Once the specified test pressure (usually 1.3 - 1.5 times the normal operating pressure) is reached, maintain this pressure for a set period, often 30 minutes to 1 hour. During this holding time, conduct a detailed visual inspection of the entire tank, including welds, seams, and joints, using non - destructive testing methods like ultrasonic or dye penetrant inspection if necessary.
Pressure Release and Final Evaluation: After the holding period, slowly release the pressure in the tank at a rate similar to the pressure increase. Once the tank returns to atmospheric pressure, re - inspect it for any permanent deformation, cracks, or other damages that may have occurred during the test. If the tank shows no signs of failure and meets all relevant standards and specifications, it can be considered passed the pressure test and deemed suitable for use. Failure to meet these requirements indicates the need for repair or replacement.
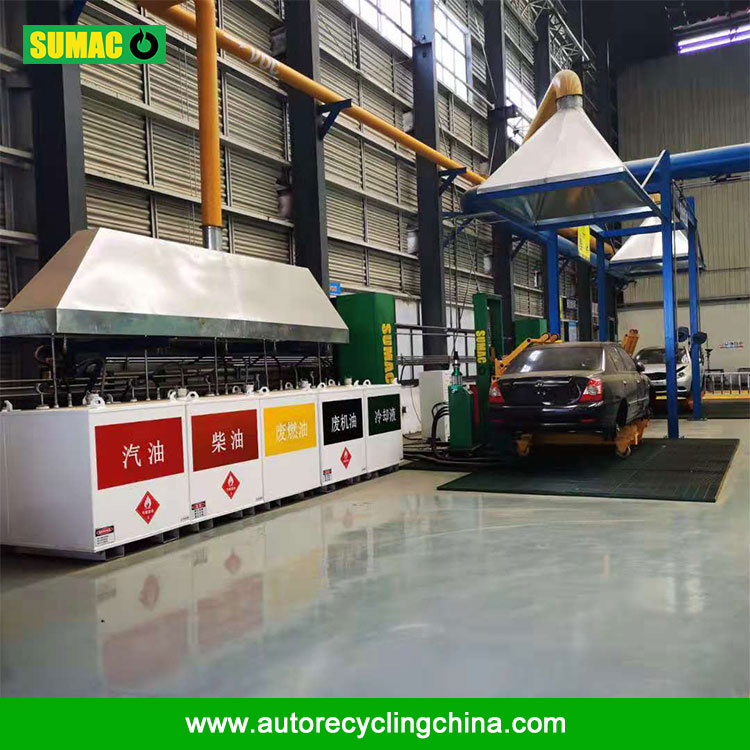