To effectively monitor the liquid level in a coolant storage tank, several smart strategies and advanced technologies can be employed. Here are some practical methods:
1. Ultrasonic Level Sensors
These sensors use ultrasonic waves to measure the distance from the sensor to the liquid surface. They are non - intrusive, meaning they can be mounted externally on the tank, which is ideal for corrosive or high - pressure coolants. Ultrasonic sensors are highly accurate and can provide continuous level monitoring. They also work well in harsh environments, as they are not affected by the coolant's chemical properties. However, they may be influenced by factors such as temperature and tank shape, so proper calibration is necessary.
2. Float - Based Level Switches
Float - based systems are simple and cost - effective. A float, which is less dense than the coolant, rises and falls with the liquid level. This movement can actuate a switch to trigger an alarm or control pump operations. These switches are easy to install and maintain, but they provide discrete level measurements rather than continuous data. They are best suited for applications where specific level thresholds need to be monitored, such as low - level or high - level alarms.
3. Capacitance Level Sensors
Capacitance sensors measure changes in electrical capacitance between the sensor and the tank wall or a reference electrode. The dielectric constant of the coolant affects the capacitance, allowing the sensor to determine the liquid level. These sensors can be used for both conductive and non - conductive coolants and are highly accurate. They are also suitable for applications with varying temperatures and pressures.
4. Radar Level Sensors
Radar sensors use microwave technology to measure the liquid level. They are highly accurate and can work in challenging environments, including those with vapor, dust, or turbulence. Radar sensors can provide continuous level measurements and are unaffected by the coolant's properties, such as density or conductivity. They are particularly useful for large - scale storage tanks.
5. Magnetic Level Gauges
Magnetic level gauges consist of a float with a magnet inside a chamber adjacent to the tank. The float rises and falls with the liquid level, and its position is indicated by magnetic flags or a pointer on the outside of the chamber. These gauges provide a visual indication of the liquid level and can also be equipped with switches for alarm or control functions. They are reliable and do not require power to operate.
6. Pressure Transmitters
Pressure transmitters measure the hydrostatic pressure at the bottom of the tank, which is proportional to the liquid level. They are suitable for both open and closed tanks and can provide continuous level measurements. However, they require calibration based on the coolant's density and the tank's geometry.
7. Smart Monitoring Systems
Integrate multiple sensors with a centralized monitoring system that uses IoT technology. This allows for real - time data collection, analysis, and remote access. Smart systems can also send alerts via email or SMS when levels reach critical points, enabling proactive maintenance and preventing issues such as overflow or pump damage.
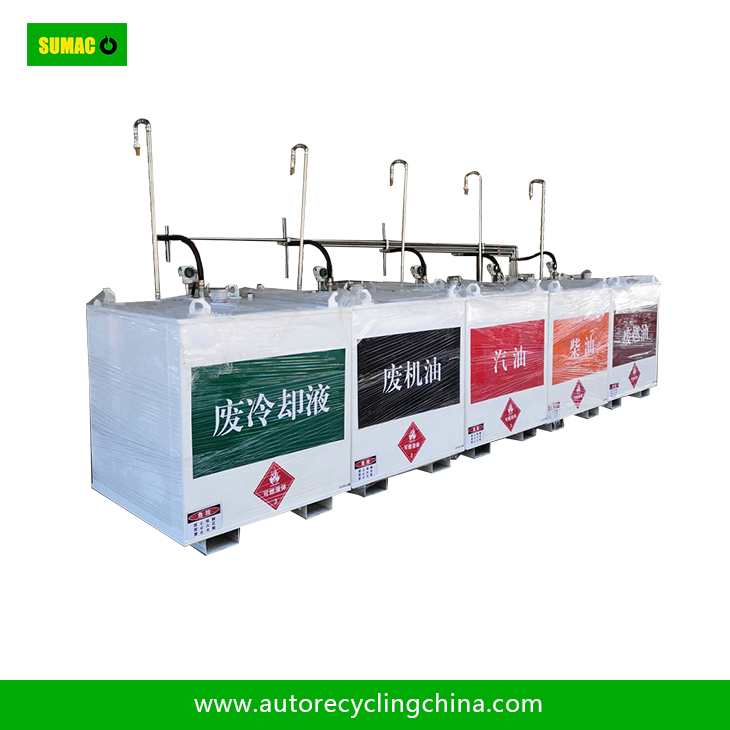