Protecting coolant storage tanks in low - temperature environments requires a comprehensive approach to prevent freezing, material embrittlement, and operational failures. Here are the key protective measures:
1. Insulation Systems
Install high - quality insulation materials such as foam glass, mineral wool, or closed - cell foam. These materials reduce heat loss and maintain the coolant temperature above its freezing point. For example, foam glass insulation offers excellent resistance to moisture ingress and can withstand extremely low temperatures without degradation. Ensure the insulation is properly sealed to prevent moisture penetration, which could compromise its effectiveness.
2. Heating Systems
- Trace Heating: Use electric heat tracing cables along the tank walls and pipelines. These cables provide controlled heat to prevent freezing. Thermostatically controlled systems ensure energy efficiency by activating only when temperatures drop below a set threshold.
- Jacket Heating: For larger tanks, consider a jacketed design with a heating medium (e.g., hot water or steam) circulating between the inner and outer walls. This method provides uniform heating and is suitable for maintaining precise temperatures.
3. Material Selection
Choose materials resistant to low - temperature embrittlement. For metallic tanks, stainless steel grades like 304L or 316L are preferred due to their excellent toughness at sub - zero temperatures. Non - metallic options such as high - density polyethylene (HDPE) or fiberglass - reinforced plastic (FRP) can also be used, as they remain flexible in cold conditions. Avoid carbon steel in extremely cold environments unless specifically alloyed for low - temperature service.
4. Monitoring and Control
- Temperature Sensors: Install sensors inside the tank and on critical external surfaces to continuously monitor temperatures. Connect these sensors to an alarm system that triggers when temperatures approach freezing points.
- Pressure Relief Devices: Ensure tanks are equipped with pressure relief valves designed for low - temperature operation. Cold temperatures can cause pressure fluctuations, and proper relief mechanisms prevent tank damage.
5. Maintenance Practices
- Regular Inspections: Check insulation for damage or moisture ingress, especially after extreme weather events. Inspect heating systems for functionality and repair any faulty components promptly.
- Drainage Management: Ensure proper drainage around the tank to prevent the accumulation of water, which could freeze and cause structural damage. Use heated drains if necessary.
6. Coolant Management
- Freezing Point Adjustment: Use coolants with additives that lower their freezing points, such as ethylene glycol or propylene glycol. Regularly test coolant concentrations to ensure they remain effective in low temperatures.
- Circulation Systems: Keep coolant circulating during cold periods to prevent stagnant zones from freezing. This may require installing pumps or agitators.
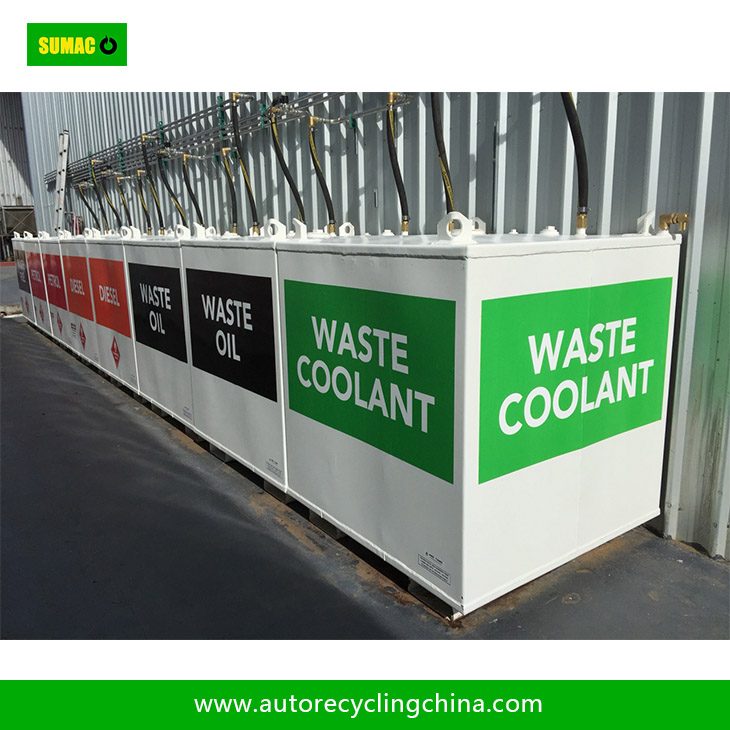