To achieve energy conservation and consumption reduction in coolant storage tanks, multiple strategies can be adopted from aspects of equipment design, operation, and management.
Efficient Insulation and Heat Preservation
Select high - performance insulation materials for the coolant storage tank. Materials like polyurethane foam or vacuum - insulated panels have low thermal conductivity, which can significantly reduce heat exchange between the coolant and the external environment. By minimizing heat loss or gain, the energy required to maintain the coolant at an appropriate temperature can be greatly decreased. For example, a well - insulated tank can reduce the frequency of heating or cooling operations, saving the energy consumed by related equipment such as heaters or chillers.
Select high - performance insulation materials for the coolant storage tank. Materials like polyurethane foam or vacuum - insulated panels have low thermal conductivity, which can significantly reduce heat exchange between the coolant and the external environment. By minimizing heat loss or gain, the energy required to maintain the coolant at an appropriate temperature can be greatly decreased. For example, a well - insulated tank can reduce the frequency of heating or cooling operations, saving the energy consumed by related equipment such as heaters or chillers.
Intelligent Control Systems
Install intelligent control systems that monitor the temperature, level, and other parameters of the coolant in real - time. These systems can adjust the operation of auxiliary equipment, such as pumps and cooling/heating devices, according to actual needs. For instance, when the coolant temperature is within an acceptable range, the system can automatically reduce the power of the heating or cooling equipment or even pause their operation. Variable - frequency drives can be used for pumps, enabling them to operate at the optimal speed according to the flow demand, rather than running at full speed continuously, thus saving a large amount of electrical energy.
Install intelligent control systems that monitor the temperature, level, and other parameters of the coolant in real - time. These systems can adjust the operation of auxiliary equipment, such as pumps and cooling/heating devices, according to actual needs. For instance, when the coolant temperature is within an acceptable range, the system can automatically reduce the power of the heating or cooling equipment or even pause their operation. Variable - frequency drives can be used for pumps, enabling them to operate at the optimal speed according to the flow demand, rather than running at full speed continuously, thus saving a large amount of electrical energy.
Optimal Equipment Configuration and Operation
Choose energy - efficient equipment for the coolant storage system. High - efficiency pumps and heat exchangers can reduce energy consumption during coolant circulation and heat transfer processes. In operation, optimize the process parameters. For example, determine the best coolant flow rate to ensure effective heat exchange while minimizing the energy consumption of the pump. Also, regularly maintain the equipment to keep it in good working condition. Clean heat exchangers to improve their heat transfer efficiency, and lubricate and repair pumps in time to reduce mechanical friction losses, all of which contribute to energy savings.
Choose energy - efficient equipment for the coolant storage system. High - efficiency pumps and heat exchangers can reduce energy consumption during coolant circulation and heat transfer processes. In operation, optimize the process parameters. For example, determine the best coolant flow rate to ensure effective heat exchange while minimizing the energy consumption of the pump. Also, regularly maintain the equipment to keep it in good working condition. Clean heat exchangers to improve their heat transfer efficiency, and lubricate and repair pumps in time to reduce mechanical friction losses, all of which contribute to energy savings.
Waste Heat Recovery and Reuse
If there are waste heat sources in the production process, consider using them to pre - heat the coolant. For example, exhaust heat from engines or industrial furnaces can be recovered through heat exchangers and used to raise the temperature of the coolant, reducing the need for additional heating energy. Similarly, the heat released when the coolant cools down can also be recovered and utilized in other processes, further improving energy utilization efficiency and achieving the goal of energy conservation and consumption reduction for coolant storage tanks.
If there are waste heat sources in the production process, consider using them to pre - heat the coolant. For example, exhaust heat from engines or industrial furnaces can be recovered through heat exchangers and used to raise the temperature of the coolant, reducing the need for additional heating energy. Similarly, the heat released when the coolant cools down can also be recovered and utilized in other processes, further improving energy utilization efficiency and achieving the goal of energy conservation and consumption reduction for coolant storage tanks.
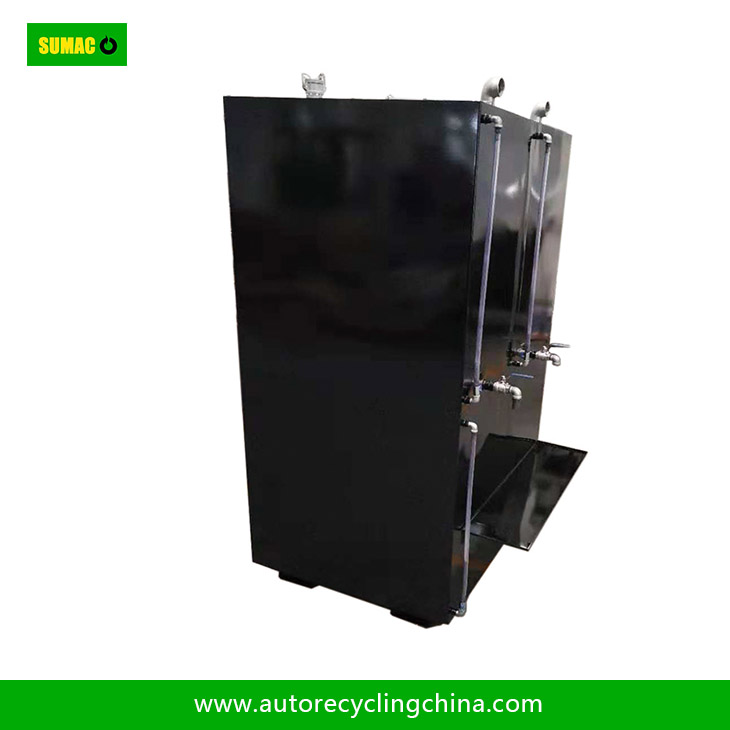